In the ever-evolving landscape of healthcare, the role of medical devices in diagnosis, treatment, and patient care cannot be overstated. Let’s delve into the intricate world of medical device manufacturing and explore the critical aspects that contribute to precision.
The Crucial Role of Precision in Medical Device Manufacturing
Precision in medical device manufacturing is synonymous with reliability, accuracy, and consistency. The demand for precision stems from the critical nature of these devices, where even a minor flaw can have profound consequences. From diagnostics to life-saving interventions, every component and process involved in manufacturing must align with stringent standards to guarantee optimal performance.
Navigating Regulatory Compliance: ISO 13485 Certification
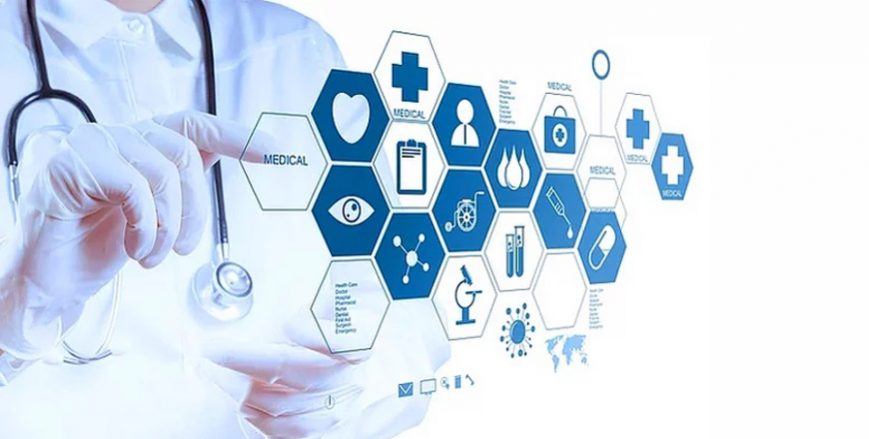
One cornerstone of precision in medical device manufacturing is adherence to regulatory standards, with ISO 13485 playing a pivotal role. The ISO 13485 certificate signifies a commitment to quality management systems specifically designed for medical devices. Manufacturers adhering to this standard demonstrate their dedication to meeting customer and regulatory requirements, emphasizing the importance of risk management and maintaining effective processes throughout the device’s lifecycle. Thus, the ISO 13485 certification stands as a testament to a medical device manufacturer’s unwavering commitment to maintaining the highest standards of quality management in the design, production, and distribution of medical devices.
Design Validation: Ensuring Functional Integrity
Precision starts at the design stage, where thorough validation is paramount. Design validation ensures that the medical device meets the specified requirements and functions as intended. This involves a comprehensive assessment of the design against user needs, intended use, and regulatory standards.
Material Selection: The Foundation of Precision
The materials used in medical device manufacturing play a pivotal role in determining the device’s performance, durability, and biocompatibility. Precision extends beyond measurements and dimensions; it involves selecting materials that meet the stringent requirements of the healthcare industry. Biocompatible materials, resistance to wear and corrosion, and compatibility with various sterilization methods are all critical considerations to ensure the device’s precision and longevity.
Supply Chain Management: Orchestrating Precision Across Borders
A seamless and reliable supply chain is essential for maintaining precision in medical device manufacturing. From raw material procurement to component assembly, every step in the supply chain contributes to the overall quality of the final product.
Quality Control and Assurance: Safeguarding Precision at Every Stage
Quality control and assurance are the linchpins of precision in medical device manufacturing. Robust quality management systems are implemented to monitor and control each stage of the manufacturing process. Inspection and testing protocols are meticulously designed to identify and rectify any deviations from the specified standards. This proactive approach not only safeguards precision but also establishes a foundation for continuous improvement.
Technological Advancements: Driving Precision to New Heights
The marriage of technology and medical device manufacturing is pushing the boundaries of precision. Advanced manufacturing techniques, such as additive manufacturing (3D printing), computer numerical control (CNC) machining, and automation, contribute to enhanced precision and efficiency.
Post-Market Surveillance: Ensuring Long-Term Precision and Safety
Precision doesn’t end with the manufacturing process; it extends into the post-market phase. Continuous monitoring of device performance, feedback from users, and prompt response to any reported issues are integral to maintaining precision throughout the device’s lifecycle. Post-market surveillance not only ensures ongoing compliance with regulatory standards but also facilitates improvements and innovations based on real-world usage and feedback.
The Human Factor: Precision in Manufacturing Personnel
Behind every precisely manufactured medical device is a skilled and trained workforce. The human factor plays a crucial role in ensuring precision at every stage of the manufacturing process. From engineers and designers to quality control professionals, each individual contributes to the overall quality and reliability of the final product. Training programs, adherence to standard operating procedures, and a culture of continuous improvement are essential elements in cultivating a workforce that understands and values precision. By investing in the skills and knowledge of manufacturing personnel, companies can fortify their commitment to producing medical devices that meet the highest standards of precision and efficacy.
Environmental Considerations: Sustaining Precision in a Changing World
As the world grapples with environmental challenges, sustainability has become an integral aspect of precision in medical device manufacturing. From reducing waste in production processes to adopting eco-friendly materials, manufacturers are increasingly considering the environmental impact of their operations. Sustainable practices not only align with global efforts to protect the planet but also contribute to the long-term precision of medical devices.
Conclusion: Elevating Healthcare Through Precision
In the realm of medical device manufacturing, precision is not a mere buzzword; it is the cornerstone of reliability, safety, and efficacy. As technology evolves and regulatory standards become more stringent, manufacturers must embrace these challenges, striving for new heights of precision in the relentless pursuit of advancing healthcare.